Blogs from Manufacturing And Industrial Supply Companies in Owasso, OK
New OSHA Residential Construction Regulation in 2011
According to data from the department's Bureau of Labor Statistics, an average of 40 workers are killed each year as a result of falls from residential roofs. As a result, the Occupational Safety and Health Administration (OSHA) recently announced new fall protection requirements for residential construction. The new directive requires all residential builders to comply with 29 Code of Federal Regulations 1926.501(b)(13). Construction and roofing companies will have until June 16, 2011, to comply with the new directive. Under 29 CFR 1926.501(b)(13) workers engaged in residential construction over six (6) feet above the ground level are to be protected by conventional fall protection. For roofers, the 25 foot, ground-to-eave height threshold no longer applies, nor do slide guards as an acceptable form of fall protection, regardless of the roof pitch or height of the roof eave. These new requirements replace the Interim Fall Protection Compliance Guidelines for Residential Construction, Standard 03-00-001 that have been in effect since 1995 and allowed residential builders to bypass fall protection requirements. Construction and roofing companies will have up to six months (June 16, 2011) to comply with the new directive. OSHA has developed training and compliance assistance materials for small employers and will host a webinar for parties interested in learning more about complying with the standard. As always, Armor Personal Protective Equipment, LLC is here to assist employers of all types remain compliant with OSHA regulations. If you are a roofing contractor struggling with the new OSHA directive please call us today for a free consultation at our offices familiarizing you and your team with fall protection products and usage. ...read more
By Armor Personal Protective Equipment, LLC March 30, 2011
Ultra Safe Retractable Goes Above and Beyond the Call of Duty
Armor Personal Protective Equipment LLC is proud to announce that we will now be stocking self retracting lifelines that are designed and tested for use in horizontal and leading edge use in addition to traditional vertical use. Ultra-Safe's line of European manufactured retractables are constructed and tested in accordance with the more stringent DIN EN 360 standards. This standard, when compared to the much more lenient OSHA requirements, more accurately addresses the real world applications many construction crews work under. DIN EN 360 Testing GraphicAll ULTRA-SAFE safety retractable's are tested in accordance with the requirements based on the new draft of DIN EN 360 and have the requisite test approvals. ULTRA-SAFE safety retractable's are certified in accordance with CE by the test and certification body of the Personal Safety Equipment technical committee. The functional ability of the retractable is guaranteed by testing them in extreme situations ( e.g.. Cold, heat, and moisture). The new draft of DIN EN 360 requires that all safety retractable's are also tested in horizontal use. In particular, falling over a sharp edge (leading edge). The tests have fully confirmed that the ULTRA-SAFE safety retractable series satisfy this new standard. The new DIN EN 360 requirements:Design and ergonomicsMaterials and constructionBlocking after pre-treatment. blocking in horizontal positionStatic load bearing capacity, static load bearing for horizontal applicationsDynamic performance, dynamic performance for horizontal applications, dynamic load bearing capacity for horizontal applicationsOptional requirement in respect to fatigue strengthCorrosion resistanceIdentification and informationOh, and just in case you were wondering…these retractable exceed current OSHA requirements!Armor PPE will stock 15′, 30′, 60′ & 100′ wire rope (3/16″) retractable lifelines that all meet the DIN EN 360 standards. You can download the full user instruction for this line of SRL's here or call Armor PPE today to receive a price quote and delivery lead time! ...read more
By Armor Personal Protective Equipment, LLC February 16, 2011
Urgent! Miller Fall Protection Responds to Recent Safety Bulletin
There has been an unendorsed "Special Safety Bulletin" in circulation regarding Miller® Fall Protection Harnesses and the integrity of our quick-connect buckles with plastic inserts. This notification is to alert you that this publication was neither issued nor approved by Sperian Fall Protection, Inc. This safety bulletin concerning our quick-connect buckles on Miller Harnesses improperly creates a question about the safety of our quick-connect buckles and potentially our harnesses. This is, of course, not true. The purpose of this memo is to state clearly that there is no stop-use or recall on any Miller fall protection harness that has a quick connect buckle with a plastic insert. The safety bulletin states that the user "Identified two units that were manufactured with a "green" plastic component in the locking mechanism that was cracked. The cracked plastic component prevented the latch from staying in a closed position. Due to this vulnerability, the manufacturer has redesigned the harness buckles using all-metal parts." While it is true that the quick-connect buckle will not stay closed if the plastic part is cracked, proper inspection prior to donning should prevent the harness from being worn. Once worn, it is very unlikely that it will become damaged and if the buckle does become damaged, as we have found through our testing, the buckle will not disconnect. The statement above also implies that the buckle was damaged during manufacturing. Sperian Fall Protection does a 100% inspection of all Miller Personal Protective products prior to shipping, thus, it is very likely that the damage occurred during handling and storage. Finally, Miller moved to the new design of the all-metal buckle because of documented problems with proper maintenance, handling and storage by users of quick-connect buckles with plastic components. We strongly recommend that customers continue their routine inspection of all fall arrest equipment according to applicable OSHA, ANSI and CSA requirements following the detailed inspection instructions outlined in the Miller user guidelines. Any harness in good condition but exhibiting signs of a fractured plastic spacer in the Miller quick-connect buckle can be returned directly for replacement. Prior to returning, please contact the Miller Technical Services Department for a Return Goods Authorization (RGA) at 800/873-5242 and press 4 for Technical Services. Michael Seman, Product ManagerSperian Safety at Height – Now a part of Honeywell ...read more
By Armor Personal Protective Equipment, LLC January 27, 2011
Reference: SRL Inspection Guide
1) Check Housing Before every use, inspect the unit's housing for loose fastenersand bent, cracked, distorted, worn, malfunctioning or damaged parts.2) Lifeline Test the lifeline retraction and tension by pulling out several feet of the lifeline and allow it to retract back into the unit. Always maintain a light tension on the lifeline as it retracts.The lifeline should pull out freely and retract all the way back into the unit. Do not use the unit if the lifeline does not retract. The lifeline must be checked regularly for signs of damage. Inspect for cuts, burns, corrosion, kinks, frays or worn areas. Inspect any sewing (web lifelines) for loose, broken or damaged stitching.3) Braking Mechanism The braking mechanism can be tested by grasping the lifeline above the load indicator and applying a sharp steady pull downward which will engage the brakes. There should be no slippage of the lifeline while the brakes are engaged. Once tension is released, the brakes will disengage and the unit will return to the retractable mode. Do not use the unit if the brakes do not engage.Check the hardware as directed in 1A under Lanyard Inspection. The snap hook load indicator is located in the swivel of the snap hook. The swivel eye will elongate and expose a red area when subjected to fall arresting forces. Do not use the unit if the load impact indicator has been activated.4) Snap Hook Check the snap hook to be sure that it operates freely, locks, and the swivel operates smoothly. Inspect the snap hook for any signs of damage to the keepers and any bent, cracked, or distorted components.5) Anchorage Connection Make sure the carabiner is properly seated and in the locked position between the attachment swivel/point on the device and the anchor point. This document is provided as an over view to fall protection equipment inspection only and is not a substitute for a complete inspection by the manufacturer or your companies competent person as defined by OSHA. This information provided by Miller Fall Protection (www.millerfallprotection.com). Always refer to the instructions for your specific fall protection equipment to ensure safety and product construction comprehension ...read more
By Armor Personal Protective Equipment, LLC January 26, 2011
Reference: Lanyard Inspection Guide
When inspecting lanyards, begin at one end and work to the opposite end, slowly rotatingthe lanyard so that the entire circumference is checked. Additionally, follow the procedures below. 1) Hardware A) Snaps: Inspect closely for hook and eye distortions, cracks, corrosion, or pitted surfaces. The keeper (latch) should seat into the nose without binding and should not be distorted or obstructed. The keeper spring should exert sufficient force to firmly close the keeper. Keeper locks must prevent the keeper from opening when the keeper closes.B) Thimbles: The thimble must be firmly seated in the eye of the splice, and the splice should have no loose or cut strands. The edges of the thimble must be free of sharp edges, distortion, or cracks.2) Wire Rope Lanyard Always wear gloves when inspecting a wire rope lanyard; broken strands can cause injury. While rotating the wire rope lanyard, watch for cuts, frayed areas or unusual wearing patterns on the wire. Broken strands will separate from the body of the lanyard.3) Web Lanyard While bending webbing over a pipe or mandrel, observe each side of the webbed lanyard. This will reveal any cuts, snags or breaks. Swelling, discoloration, cracks and charring are obvious signs of chemical or heat damage. Observe closely for any breaks institching. Inspect lanyard warning flag for signs of activation. Titan tubular lanyards must be measured to determine activation.4) Rope Lanyard Rotate the rope lanyard while inspecting from end-to-end for any fuzzy, worn, broken or cut fibers. Weakened areas from extreme loads will appear as a noticeable change in original diameter. The rope diameter should be uniform throughout, following a short break-in period.5) Shock Absorber Pack The outer portion of the pack should be examined for burn holes and tears. Stitching on areas where the pack is sewn to D-rings, belts or lanyards should be examined for loose strands, rips, deterioration or other signs of activation.6) Shock-Absorbing Lanyard Shock-absorbing lanyards should be examined as a web lanyard (described in item 3 above). However, also look for the warning flag or signs of deployment. If the flag has been activated, remove this shock-absorbing lanyard from service. This document is provided as an over view to fall protection equipment inspection only and is not a substitute for a complete inspection by the manufacturer or your companies competent person as defined by OSHA. This information provided by Miller Fall Protection (www.millerfallprotection.com). Always refer to the instructions for your specific fall protection equipment to ensure safety and product construction comprehension ...read more
By Armor Personal Protective Equipment, LLC January 26, 2011
Reference: Safety Harness Inspection Guide
Regularly we are asked what to look for when inspecting full body harnesses and body belts. In response, we have posted Miller Fall Protection's Harness (and Body Belt) InspectionGuide. 1) Webbing Grasp the webbing with your hands 6 inches (152mm) to 8 inches (203mm) apart. Bend the webbing in an inverted "U" as shown. The surface tension resulting makes damaged fibers or cuts easier to detect. Follow this procedure the entire length of the webbing, inspecting both sides of each strap. Look for frayed edges, broken fibers, pulled stitches, cuts, burns and chemical damage.2) D-Rings/Back Pads Check D-rings for distortion, cracks, breaks, and rough or sharp edges. The D-ring should pivot freely. Inspect for any unusual wear, frayed or cut fibers, or broken stitching of the D-ring attachments. Pads should also be inspected for cracks, excessive wear, or other signs of damage.3) Buckles Inspect for any unusual wear, frayed or cut fibers, or broken stitching of the buckle attachments.4) Tongue Buckles/Grommets Buckle tongues should be free of distortion in shape and motion. They should overlap the buckle frame and move freely back and forth in their socket. Roller should turn freely on frame. Check for distortion or sharp edges. Inspect for loose, distorted or broken grommets. Webbing should not have additional punched holes.5) Friction and Mating Buckles Inspect the buckle for distortion. The outer bars and center bars must be straight. Pay special attention to corners and attachment points at the center bar.6) Quick-Connect Buckles Inspect the buckle for distortion. The outer bars and center bars must be straight. Make sure dual-tab release mechanism is free of debris and engages properly.7) Harness Fall Arrest Indicators Inspect fall arrest indicators (located on the back D-ring pad) for signs of activation. Remove from service if broken or stretched between any of the four (4) pairs of arrows. This document is provided as an over view to fall protection equipment inspection only and is not a substitute for a complete inspection by the manufacturer or your companies competent person as defined by OSHA. This information provided by Miller Fall Protection (www.millerfallprotection.com). Always refer to the instructions for your specific fall protection equipment to ensure safety and product construction comprehension. Related Articles Best Practices to Save Money on Fall Protection (oklahomasafetysupply.com) ...read more
By Armor Personal Protective Equipment, LLC January 26, 2011
OSHA Withdraws Residential Construction Fall Protection Loophole
Originally posted December 28, 2010 by Seth Newell @ Real Safety: A Blog by Armor PPE US Labor Department's OSHA acts to protect residential roofing workersAgency rescinds Clinton-era directive and gives workers more safeguards against falls December 22, 2010 – OSHA today announced a new directive withdrawing a former one that allowed residential builders to bypass fall protection requirements. This new directive replaced the 1995 ‘Interim Fall Protection Compliance Guidelines for Residential Construction, Standard 03-00-001′ that addressed concerns of feasibility of fall protection in residential construction. 1995′s Interim Fall Protection Compliance Guidelines for Residential Construction, Standard 03-00-001 allowed employers engaged in certain residential construction activities to use specified alternative methods of fall protection rather than the conventional fall protection required by the residential construction fall protection standard. Since 1995, it seems that OSHA and related industry experts have seen enough advancements in fall protection engineering and product design to now feel that feasibility is no longer an issue. According to the U.S. Department of Labor Release Number: 10-1753-NAT, an average of 40 workers are killed each year as a result of falls from residential roofs. That is roughly 1 worker every 9 working days! "Fatalities from falls are the number one cause of workplace deaths in construction. We cannot tolerate workers getting killed in residential construction when effective means are readily available to prevent those deaths," said Assistant Secretary of Labor for Occupational Safety and Health Dr. David Michaels. "Almost every week, we see a worker killed from falling off a residential roof. We can stop these fatalities, and we must." With the issuance of the new residential fall protection directive, all residential construction employers must comply with 29 Code of Federal Regulations 1926.501(b)(13). Where residential builders find that traditional fall protection is not feasible, 29 CFR 1926.501(b)(13) still allows for alternative means of providing protection…although the proof of feasibility is still the burden of the employer. While this new directive will be wildly unpopular with many home builders and will undoubtedly eliminate a number of small home builders, the overall effect should be a positive one. There is no cost that can be put on a human life and the minimal increase in costs home builders and buyers will see should be easily offset by smart planning, waste elimination and simply buying smart. Scan to view our Google Places Page for contact information Information obtained from: www.OSHA.govRelease Number: 10-1753-NATDec. 22, 2010 Armor Personal Protective Equipment, LLC offers a wide variety of safety equipment to properly address work site hazards of any kind. If you are a home builder or residential construction contractor, please feel free to contact us for quotations or product needs identification that can keep you compliant and profitable. Contact us Today!Sales@armorppe.com [Phone] 918-376-4299 ...read more
By Armor Personal Protective Equipment, LLC January 13, 2011
Don't wait until the ice gets here, get Ice Cleats now!
Armor PPE now has stock on Trex Ice Traction cleats. These amazing little slip on cleats provide sure footing on packed snow and ice and are still small enough to fold up and store in a sandwich baggie! With the Trex Ice cleat there will be no more scary and embarrassing slips on your trek across your frozen parking lot to the office for you! Ergodyne's one-piece ice cleat traction device for shoes or boots are easily installed and work perfectly. This ice cleat delivers excellent grip and stability on icy and snow packed surfaces. Rugged steel studs for superb grip&stability; Stretchable rubber for fit and easy on/off Flexible to -40F (-40c) Each set comes with 2 replacement studs (additional replacements are available!) Sized for a better fit Mens Sizes: Medium (5-8), Large (8-11), XL (11-14) Why spend thousands at the hospital for a broken bone? A measly $14.95 can prevent the whole experience? Don't wait until it is too late! Trex cleats are available now at www.armorppe.com. Go buy a set now! ...read more
By Armor Personal Protective Equipment, LLC January 05, 2011
They have the PPE you want, but can they service you after the sale?
Originally posted on September 15, 2010 by Seth Newell at armorppe.wordpress.com In today's economy, value for your dollar is everything. And with every hardware store and their cousin selling personal protective equipment, it is easier than ever to find great deals on quality products from manufacturer‘s you recognize. A word of caution however; technical products such as respiratory protection and fall protection are extremely troublesome to end users when purchased through wholesale avenues. My point in these statements is this: not every seller of a given product is an authorized distributor and by purchasing through these two-step suppliers, you are severely short-changing your safety program. There are a number of wholesale suppliers out there injecting themselves between the manufacturer and your local supplier. There is nothing wrong with this per se; there is a time and a place for wholesale purchases. Technical products where severe personal injury or death is the risk is no place for these groups however. By utilizing these sources factory support and service on goods may oftentimes not be available to your company. Especially where high dollar and high liability items such as fall protection or respiratory protection come into play, technical support and customer service from the people who designed the product is extremely important. After all, lives are on the line quite literally! I recently discovered a large client who had purchased well over $75,000 worth of brand name fall protection equipment from a supplier whom it was assumed was an authorized distributor. He had, in fact, sold a large amount of this very same equipment to another local company the previous year with no known complications. The client received very competitive pricing and the product showed up on time and new as promised. After a few months, I approached this client about a new program that would allow him to get free training by leveraging future purchases of the very same manufacturers goods. All that was required of this client was to continue to buy PPE required by OSHA. Where it made sense, the client would be asked to make sure the products purchased were those made by this particular manufacturer and from an authorized distributor who would track the purchases on the client's behalf. Many of you can already see where this is going, I am sure. The client felt that his large purchase of fall protection only a couple of months earlier should be retroactively included. Understandably, he wanted to take advantage of the $4,000 in free training that would have been available. Chances are, these purchases would have been included if they were purchased from an authorized distributor. Unfortunately, the seller of these goods was not an authorized distributor but rather a suave salesman with access to very competitive pricing through wholesale means. To add insult to injury, it was also discovered that the client did not receive the factory training for the units he purchased. Rather than spend a whole week figuring out how things worked, this client could have received free training from a factory trained specialist who would have been flown to his facility to give one on one instruction to the competent persons who would be responsible for the erection and disassembly of this equipment. Just because a supplier can get a product, doesn't mean they can get you technical support and help when you need it. We all know being stranded just isn't fun. When millions of dollars are on the line and your job schedule is tight, authorized distributors are your best friends. We know the contacts, we know the details and we have the pull that gets your problems solved quickly. No matter your industry, be proactive and make sure your suppliers are authorized distributors for the highly technical products your company uses every day. You will save money in the long run! ...read more
By Armor Personal Protective Equipment, LLC October 21, 2010
Commissioned Sales - Industrial/Construction Safety Equipment
Local industrial/construction safety company seeks outgoing motivated self starter with background in construction, industrial manufacturing or business to business sales. Commissioned sales paid monthly. Commission paid on percentage of monthly gross profit for sales in your territory. Full time and part time opportunities available. Reply to: job-zhw23-1943557316@craigslist.org Location: Tulsa OK&NE Oklahoma Area Compensation: 100% Commissioned Sales. Paid Monthly. Commission rate determined by skills set. Telecommuting is ok. This is a part-time job. This is a contract job. Principals only. Recruiters, please don't contact this job poster. Please, no phone calls about this job! Please do not contact job poster about other services, products or commercial interests. ...read more
By Armor Personal Protective Equipment, LLC September 15, 2010
OSHA seeks members for construction workers' safety committee
OSHA is seeking nominations for individuals to serve on the Advisory Committee on Construction Safety and Health. The committee advises the Secretary of Labor on developing standards and policies that affect the safety and health of construction workers. ACCSH and OSHA's Assistant Secretary have consulted for nearly 40 years on construction safety issues such as women in construction, recordkeeping, crane safety, and safety and health resources for Latino construction workers. OSHA seeks nominees with experience and expertise in construction-related safety and health issues. In support of the Department of Labor's commitment to equal opportunity in the workplace, the agency is also interested in women and individuals from diverse ethnic backgrounds to serve on the committee. Selected nominees will fill eight vacancies in employee, employer, public and state safety and health agency representative groups. Nominations may be submittedonline, or by mail or fax by the Nov. 12 deadline. See theFederal Registernoticefor more information. ...read more
By Armor Personal Protective Equipment, LLC September 15, 2010
They have the PPE you want, but can they service you after the sale?
In today's economy, value for your dollar is everything. And with every hardware store and their cousin selling personal protective equipment, it is easier than ever to find great deals on quality products from manufacturer's you recognize. A word of caution however; technical products such as respiratory protection and fall protection can be extremely troublesome to end users when they are purchased through wholesale avenues. My point in these statements is this: not every seller of a given product is an authorized distributor and by purchasing through these two-step suppliers, you are severely shortchanging your safety program. There are a number of wholesale suppliers out there injecting themselves between the manufacturer and your local supplier. There is nothing wrong with this per se; there is a time and a place for wholesale purchases. Technical products where severe personal injury is the hazard is no place for these groups however. By utilizing these sources factory support and service on goods obtained through this avenue could not be available to your company. Especially where high dollar and high liability items such as fall protection or respiratory protection are concerned, technical support and customer service is extremely important. After all, live are on the line…quite literally! I recently discovered a large client who had purchased well over $75,000 worth of brand name fall protection equipment from a supplier whom the client assumed was an authorized distributor of the equipment in question. He had, in fact, sold a large amount of this equipment to another local company in town with no known detriment. The client got an excellent price and the product showed up as new as promised. After a few months, I approached him about a new program that would allow this client to obtain free training from this very same manufacturer in exchange for signing up for a rewards program that would cost him nothing extra. All that was required of this client was to continue to purchase PPE that was required anyway. Where it made sense, the client would be asked to ensure the products purchased were those made by this particular manufacturer and from and authorized distributor who would track these purchases on the clients behalf. Many of you can already see where this is going, I am sure. Suffice it to say, the client felt that his large purchase of fall protection should be retroactively included. Understandably, he wanted to take advantage of the $4,000 in free training that could have been made available and chances are, these purchases would have been included if they were purchased from an authorized distributor. Unfortunately, the supplier was not. To add insult to injury, it was also discovered that the client did not receive the factory training for the units he purchased. Rather than spend a whole week figuring out how things worked, this client could have received free training from a factory trained specialist who would have flown to his facility to give one on one instruction to the competent persons who would be responsible for the erection and disassembly of this equipment. Now, before you get upset with the manufacturer in this tale, you should know that they made the situation right for the customer. His crews will be receiving the training that would have been immediately available had the product been purchased from an authorized distributor. The point of this little tale is that the client spent more money on this system by not ensuring that his supplier was an authorized distributor. Just because a supplier can get a product, doesn't mean they can get you technical support and help when you need it. We all know being stranded just isn't fun. When millions of dollars are on the line and your job schedule is tight, authorized distributors are your best friends. We know who to contact with questions. We have the pull that gets your problems solved quickly. Many times authorized distributors also have the aptitude and knowledge that helps you keep people safe while they work. No matter your industry, be proactive and ensure your suppliers are authorized distributors for the highly technical products your company uses every day. You will save money in the long run! ...read more
By Armor Personal Protective Equipment, LLC August 23, 2010
Class II now required on Manhattan Construction's Tulsa (Area) sites
It has been the standard in many other locations across the country, but here, in our little corner of the map, mandatory high visibility garments on on-site has only been a good idea. That was the past. This is the now. By requiring that all personnel on-site wear a minimum of Class II high visibility garments, Manhattan Construction has taken a big step forward in reducing low-visibility related incidents. Additionally, Manhattan may indirectly have forced the hand of some slow to comply (or simply non-compliant) sub contractors thus increasing safety for us all. ...read more
By Armor Personal Protective Equipment, LLC July 01, 2010
Gatorade Announces Allocations for Powder Mix
For many of you dealing in Gatorade, you may or may not be aware of allocations that have already been put into place. According to a notice received from Gatorade on 6/17/2010, Gatorade 21-oz (2.5 Gallon) and 51-oz (6 Gallon) packaging distributors will be allotted a certain quantity of product based on Gatorade's current usage, Gatorade's forecast usage, and product availability. The hot time of the year is well on its way and keeping cool and hydrated just gotA LOTmore complicated. ...read more
By Armor Personal Protective Equipment, LLC June 24, 2010
Read The Latest Newsletter from Armor Personal Protective Equipment
We've just published a new edition of our newsletter! You can check it out on our website and get the latest information from Armor Personal Protective Equipment. Let us know what you think! Read It Now Here ...read more
By Armor Personal Protective Equipment, LLC June 24, 2010
Recent Reviews View all
Armor Personal Protective Equipment, LLC

By BSH DESIGNERS INC June 14, 2010
Your products and services are not only required by OSHA but vital to the safety of every construction worker. Your company being local provides a much needed service to every contractor. So, keep up the good work! ...read more
Newton Feed & Western Supply
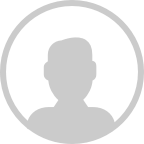
By Chris K. at Judy'sBook August 07, 2005
I have driven by this store for months before I stopped by, it always looked rather deserted as the outside signs could use a fresh coat of paint. I am happy I finally took the time to stop in. They have a great selection of supplies for t... ...read more