Top Real Estate Inspectors in Edmond, OK 73013
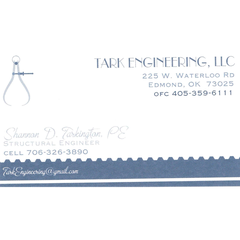
Recent Reviews View all
top roof
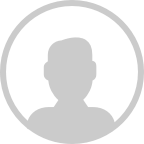
By Gilbert D. at Judy's Book January 18, 2013
Good roofing! ...read more
Castlekeep Inc
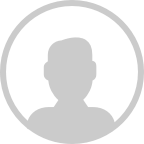
By TATanda January 13, 2013
This man had no intention of honoring the warranty. Took 5 weeks to get him out to look at a problem caused by rain damage that he had missed on the inspection. He said it had to have been from recent rain - altho,we had had no rain for months. He argued and asked me if I were a meteorologist. He was rude, offensive, and a arrogant man. He said I'd have to sue him. Avoid at all costs. Additionally, my realtor got a kick back for referring him. Bad business. ...read more
Castlekeep Inc
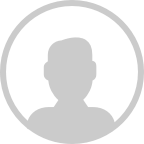
By Paul Paris July 04, 2010
Our realtor had recommended a home warranty company, so we went with Castlekeep. No matter what happened over the next four years, though, they claimed that they weren't liable. (Maybe one time they replaced a wax seal on the base of the toilet. That's all in four years of paying hundreds of dollars every year.) Why bother hiring a home warranty company if they weasel out via fine print every time you have a claim? When we called to cancel our service, they just said, "Oh, O.K." -- as though they heard our kind of complaint fairly often. What a joke. ...read more
New Photos 22 photos
View all 22Blogs View more
Roofing Maintenance
Roofing Maintenance The following information is reprinted from Roofing: Design, Criteria, Options, Selection by R. D. Herbert, III. Warranties The terms guarantee and warranty are used interchangeably in the industry; there is no legal distinction between them. The term warranty is most often used today. Full value warranties cover both materials and workmanship. Material warranties or limited warranties cover only the materials used. In limited warranties, the manufacturer takes no responsibility for the application of the materials, and is responsible only for the failure of the product itself to keep the building watertight (prevent leaks) for a specified period of time. Proration The manufacturer’s liability decreases during the warranty period, or is prorated, depending on how much of the total term of the warranty has expired. The manufacturer assumes a proportional percentage of the materials’ replacement costs, if the manufacturer’s inspection has proven that the roof was properly installed. Problems Not Covered Implied warranties as to the fitness of a material for a particular purpose are specifically denied. Consequential damages are normally excluded as well. Most manufacturers do not warrant against discoloration of their product caused by environmental conditions such as dirt, pollution, or biological agents. Loss of granules, delamination, and other similar problems are not covered by the warranty, unless the roof is leaking. Metal flashing, such as gravel stops, is usually excluded from the warranty, unless furnished by the manufacturer. This can lead to problems when leaks develop at the roof’s edge. Some systems specifically exclude applications in which exposure to oil contamination or high winds is likely. Heavy roof traffic might also rule out coverage of some systems. All warranties cover only materials furnished by the manufacturer. Some manufacturers refuse to warranty their roofs when installed over another manufacturer’s roof insulation. Reliability A new manufacturer may not have the financial reserves to cover the obligations assumed in warranting its new products. This is the most important factor in determining the value of a warranty. If the manufacturer is a relative newcomer or is undercapitalized, the warranty has little worth to the building owner. Manufacturers are continually searching for ways to improve their systems and increase dependability. Specification changes are published periodically for use by installing contractors. The National Roofing Contractors Association (NRCA) publishes the Roofing Materials Guide, which updates information on roof membrane warranties. Avoiding Roofing Failure In addition to preventive maintenance procedures to ensure the durability of roofing systems, the following guidelines address common causes of roof deterioration and possible solutions. Traffic Damage Equipment service personnel are not usually aware of the roof membrane’s susceptibility to damage, and may transport heavy equipment and materials across the roof without adequately protecting it. This traffic, along with dropped tools or equipment, often punctures the membrane or creases it enough to cause an eventual split. These breaks create a path by which moisture may enter the insulation below. The introduced moisture can also initiate blistering of the membrane, as moisture becomes trapped between the membrane and the insulation and is transformed into water vapor by solar radiation, creating high vapor pressures. Facility managers can minimize problems caused by traffic by specifying and/or installing protective walkways. Protective pathways should be located between all roof access points and any rooftop equipment or other areas requiring regular service or access. Each type of roofing requires its own type of protective walkway and installation. The best source of information is the manufacturer’s published installation guidelines. Roof Drainage It has become a basic principle within the construction industry that flat or “dead level” roof decks are not acceptable designs. Manufacturers of roofing materials state, as a general requirement, that roofs should allow for proper drainage. Unfortunately, many design professionals continue to locate drain inlets or scuppers adjacent to columns or on frame lines at the building’s perimeter. Over time, these areas tend to become the highest points in the roof when the deck deflects under structural or live loads. This deflection leads to ponding on the roof, thereby compounding the problem of insufficient drainage. Vegetation can become established in the ponds, its roof membrane, and the underlying insulation or deck. This moisture, when combined with solar radiation, causes the asphalt to emulsify, drawing the vital waterproofing oils out of the membrane. This bond break also puts increasing stress on the felt, which, due to its relatively low tensile strength, eventually splits. To decrease the possibility and/or severity of ponding, designers, installers, and maintenance personnel must make roof drainage a priority. Adapted with permission fromPreventive Maintenance for Multi-Family Housing, by John C. Maciha, available from RSMeans. ...read more
By Preferred Commercial Property Inspections July 22, 2015